Case Study
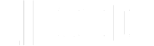
AI driven - Just in time inspection for real time defect detection
Published on 30th July 2021 | By LINCODE
For

TVS motors
Tags
Improved productivity
Quality check
Visual Quality Inspection
Defect Detection
Manufacturing
Automotive
Challenges
Inability to detect defects in real time at the point of defect, which lead to more production cost due to continued enhancement in the production process of the defective part, delayed production and increased labor cost to deal with defective product
Solutions
The Lincode Visual Inspection System (LIVIS) is their flagship Industry 4.0 solution that enabled TVS to identify surface defects, identify and measure individual components, and generate real-time data about products on the production line. By leveraging AI and deep learning, Lincode was able to capture many false-positives and false-negatives including the untrained defects in products like:
- Automotive Axles - Metallic shaft is inspected for various surface defects like scratch, dent, nicks, surface cleanliness, etc.
- Automotive Tyres - Tyres are inspected for surface defects
- Automotive Catalyst- The catalyst is inspected using a semi automated setup where the part shall be inspected completely 360 degrees.
- Automotive Sealant - To inspect for breakage and count of sealant on vehicle door liners, minimum and maximum width of the sealant, waviness of the sealant, the distance from the edge to placement of the sealant
Key Metrics
50%
Increase in overall production efficiency by upto 50%
20%
Reduction in labor cost by upto 20%
400%
ROI of 400% achieved in the first 6 months of deployment