Case Study

Reduce working capital requirement by optimizing production mix and supply chain
Published on 30th July 2021 | By Throughput INC
For
Multiple corporates
Tags
Industrial automation
Real time monitoring
Machine utilization
Supply chain efficiency
Manufacturing
Automotive
Optimise working capital gap
Challenges
- Large Industrial Operation with 100+ facilities called ThroughPut to examine machine behavior around uptime and downtime to improve quarterly output potential
- Operations Manager needed to propose an improvement plan to reduce $500,000 annually by reducing machine unplanned downtime
Solutions
ThroughPut’s ELI software connected with existing sensor data and provided additional sensors:
- To Measure Uptime for Individual Equipment Across 3 shifts
- Flag Downtime occurrences and compare with historical data around number of events
- Quantify dollars lost from unplanned downtime
Key Metrics
25-30%
ThroughPut’s software discovered that critical tools had on average 25-30% downtime per shift, with shift 3 being the highest
5%
5% reduction in unplanned downtime was achieved by real-time monitoring and addressing root causes which equated to $1.5M savings
15%
15% of the unplanned downtime was due to maintenance coding and unskilled workforce performing tasks on the tool
Similar Case Studies
For
World-leading supplier of switches, electronic modules and sensors
Production Monitoring
Production efficiency
Manufacturing
Production optimization
For
Global leader in manufacturing fueling and convenience store equipment
Procedure digitization
Track and Trace
Document compliance
Manufacturing
Warranty claims
For
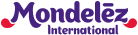